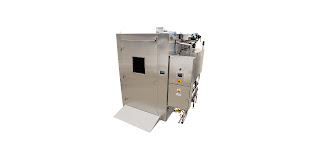 |
Laboratory animal cage washing equipment presents a number of challenges for successful installation. Image courtesy Girton Mfg. |
Laboratory animal cage and rack washers are major equipment items in the facilities where they are installed. A successful installation that enables the washer to provide rated performance for a long service life requires consideration of a host of items.
Size and Weight - These machines are large, by any measure. They are very heavy and often require special equipment and trained riggers to get them into place. Moving the washer across existing floor surfaces, because of the weight of the machine, can cause damage if not done properly. It is also necessary to plan a route from the point of unloading to the point of installation. Clear access for machine sections and any required transporting gear is needed. It may be necessary, and is often possible, to have a machine fabricated in sections that make transport through the building easier.
Material - Washing machines are fabricated of stainless steel, making them potential destroyers of almost any finished surface in a building along the transport path. It may be prudent to install protective coverings over finished surfaces during transport of the equipment from unloading area to installation space.
Utility Requirements - Laboratory animal cage washers are intended to disinfect the wash load, with carefully designed processing protocols to assure consistent levels of quality. This requires the attainment of minimum wash and rinse temperatures, along with the normal operation of every component of the machine. There are pumps, motors, air driven components, valves and a whole range of other components. Utility requirements for steam, water, electricity, compressed air, drain and possibly other services must be carefully coordinated with services available in the facility. The recommended capacity and other characteristics for each service will be clearly stated on approval documents and should be adhered to, without compromise.
Service Access - Cage and rack washers are heavy duty equipment with many mechanical parts. Service and maintenance is required on a regular basis to keep the washer in good operating order. Make sure the installation space is not too tight. Allow access for a service technician to work safely and effectively. The manufacturer, as well as the facilities manager, can provide guidance on minimum service access clearances.
Structural Requirements - There are several installation schemes for cage and rack washers. One involves recessing the washer in the floor to provide a level loading and unloading path. A pass-thru washer will require a barrier wall to separate the load and unload areas. The weight of the machine must be accommodated by the building structure at the installation site. Dimensions for a recessed installation area, or pit, need to be coordinated closely between machine manufacturer and construction trades.
Much of what is outlined here is applicable to cabinet type and tunnel washers, too. Share your plans with a
washing equipment specialist for assistance in attaining a successful outcome.